Most of the work I'd done over the years was typical hospital/clinic work. You get sick, you go see your Doctor and any samples were sent to the lab where I would stick them in an analyzer, do a kit test, look at it under a microscope or send it off to a larger lab for other tests. Microbiology & Parasitology at Smith-Kline, Hematology at Baylor Medical Center, GC/Chlamydia project research at Wi State Lab of Hygiene, solo tech during 3rd shift at Beloit Memorial Hospital, Urgent Care Tech (mostly urine, strep tests and blood counts) and finally antibody production at Harlan Sprague Dawley. Nothing I did was too dangerous but proper procedures and sterility were derigeur.
I was more than interested in working at one of our jobs, the Influenza Research Institute when I found out we had the work. It is really interesting to see things I'd always taken for granted. It's like having x-ray vision and a time machine at times. I can visualize the space as finished product with people at the benches without closing my eyes. I know the others working on the job think I'm a looney but I'd love to work in a lab like this, and not because everything is new and sparkly.
The researcher intended for this facility, Yoshihiro Kawaoka, has a history of doing research on the edge. He's quite well known for his work with the 1918 strain of influenza. folks are being told he'll be doing bird flu work.
I dunno...
But, I don't work in labs, I just build them. Everything about this job is complex. There are many redundant features but it is designed just shy of BSL-4 safety. Think Dustin Hoffman in "Outbreak." Only safer.
All the contols, air vents, fluid monitoring, temperature control, incubator control and alarms are Honeywell which I either wired, installed or helped install or wire. Honeywell sent their two US representatives, yes, they only have two for the whole country, to give us a hand. Then they sent a programmer from India and they spent a week trying to get the system to fail. Why do we deserve the attention? Most other control installers call Honeywell with issues when they've failed to wire something properly or there's been a field-related mistake. When we call Honeywell it is for something so bizarre tey've not seen it before even in their testing labs. We never, and I do mean never, have a field-error. By that I mean we wire everything correctly. By that I mean we don't have customer service calls like...
"I can't get my cable TV to work."
"Is the TV plugged in?"
"I can't tell"
"what do you mean?"
"the city is blacked-out and the lights don't work..."
Plus, when we placed the material order they wondered what we were going to do with so many controllers, sensors and other devices. Turns out this job is not just the most complex in the state, it's the most complex Honeywell has ever had a certified contractor tackle. Even the HVAC contractor, NAMI, bit off more than they could chew. All the discharge duct work, as in all the air being removed from the rooms, is welded stainless steel ductwork. Including the offices. Previously the sum total of NAMI's stainless duct installation was limited to ventilation ducts over stoves and kitchens. 20-30 feet maximum and simply vented out the nearest wall into an alley. At IRI everything returns through multiple HEPA filters, sealed in welded stainless duct before exiting the building. All the incoming air is similarly filtered, as is the water. The air is circulated via an air handler. Normally a building of 20,000 square feet would have one (1) air handler. IRI has six (6). That's roughly 3 per floor. There are monitoring sensors in every room, duct branch and system. Wire is hanging or bundled down halls everywhere.
I really enjoy the job even if the overtime cuts into training time. At least the time and a half pays for races and parts.
More images next week if I get the chance. Sorry for the poor quality, that's as good as it gets with the phone.
Part of the open bench space like any other lab.

Inside the BSL-3AG area. Here's where they will have the ferrets, chickens and "NHP's" aka non-human primates that have been exposed to virus'.
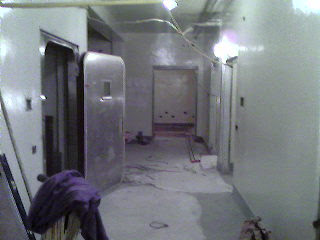
Waste decontamination unit. Anything liquid or solid that can be put into plumbing passes through this. It is essentially a large autoclave. Everything from the handwash sinks, bathrooms, showers, floor drains or utility sinks is held in this tank, pressure and heat are applied which sterilizes everythingand then it passes into the city sewer. Nothing escapes. Even the plumbing buried under the foundation is sleeved with a clear plastic pipe containing an open circuit. if there is a leak in the plumbing it connects the two wires closing the circuit and an alarm is registered in our control panel. There will be no "seepage" into the soil.


The big panel on the left came with the unit. The 12" x 12" panel on the right I installed for the controls and alarm.

For scale, that's a 12 foot ladder piled on the right. Ceilings are roughly 15 feet high. This room is 6 feet below grade underneath the main portion of the BSL-3AG lab. The walls are thick enough I wouldn't worry about any "accidents."

All the plumbing is stainless steel and all the joints are welded. No leaks and everything is pressure tested.

Turn your monitor 90 degrees and what you are looking at is a sterility hood. Above it is the return air (discharge air) ducting whic goes into the mechanical room above.
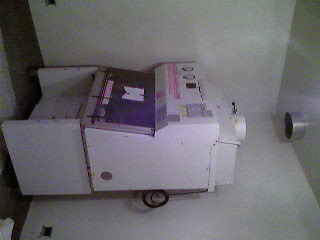
No comments:
Post a Comment